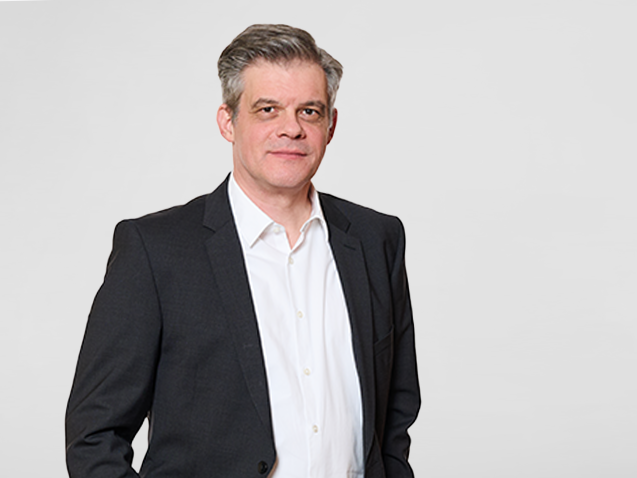
Absicherung von Produktprofit im Produktionszeitraum
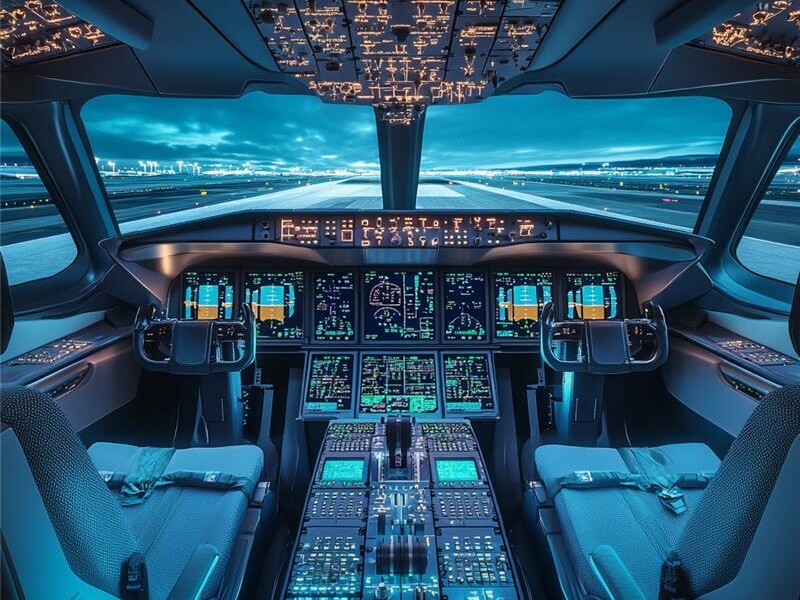
Aktuell stehen die Unternehmen der verarbeitenden Industrie aufgrund der wirtschaftlichen Randbedingungen – stagnierende Märkte, steigender globaler Wettbewerb, Unsicherheit in den Lieferketten, steigende Energiepreise, aber auch komplexere Anforderungen an das Produkt seitens der Kunden sowie kürzere Produktlebenszyklen – vor wachsenden Herausforderungen und benötigen daher deutlich mehr Transparenz für den Ergebnisbeitrag einzelner Produkte: Liefert ein Produkt einen Beitrag für den Unternehmenserfolg und in welcher Höhe?
Doch wie lassen sich unter diesen Bedingungen sichere Entscheidungen treffen, wenn der tatsächliche Ergebnisbeitrag einzelner Produkte oft im Dunkeln bleibt? Viele Unternehmen kämpfen mit lückenhaften Kalkulationen und ungenauen Zuordnungen – eine riskante Basis in Zeiten, in denen jede Fehlentscheidung teuer werden kann.
Es ist an der Zeit, genauer hinzusehen: Wie lässt sich die Profitabilität eines Produkts über seine gesamte Produktionszeit hinweg sicherstellen?
Wie lässt sich ein Controlling pro Produkt mit einfachen Mitteln schrittweise modular aufbauen?
Betrachtet man das Controlling in den Unternehmen wird auf unterschiedliche Weise der Beitrag der einzelnen Produkte zum Betriebserfolg ermittelt. Dies reicht von einer einfachen Kalkulation zur Preisbildung vor Vertragsabschluss mit dem Kunden bis zu einem Controlling der Ist-Kosten mittels Nachkalkulation. Im besten Fall liegt eine Ermittlung des jeweiligen Gewinns und Deckungsbeitrags über den gesamten Produktionszeitraum von Produktionsstart (SOP) bis zum Produktionsende (EOP) vor.
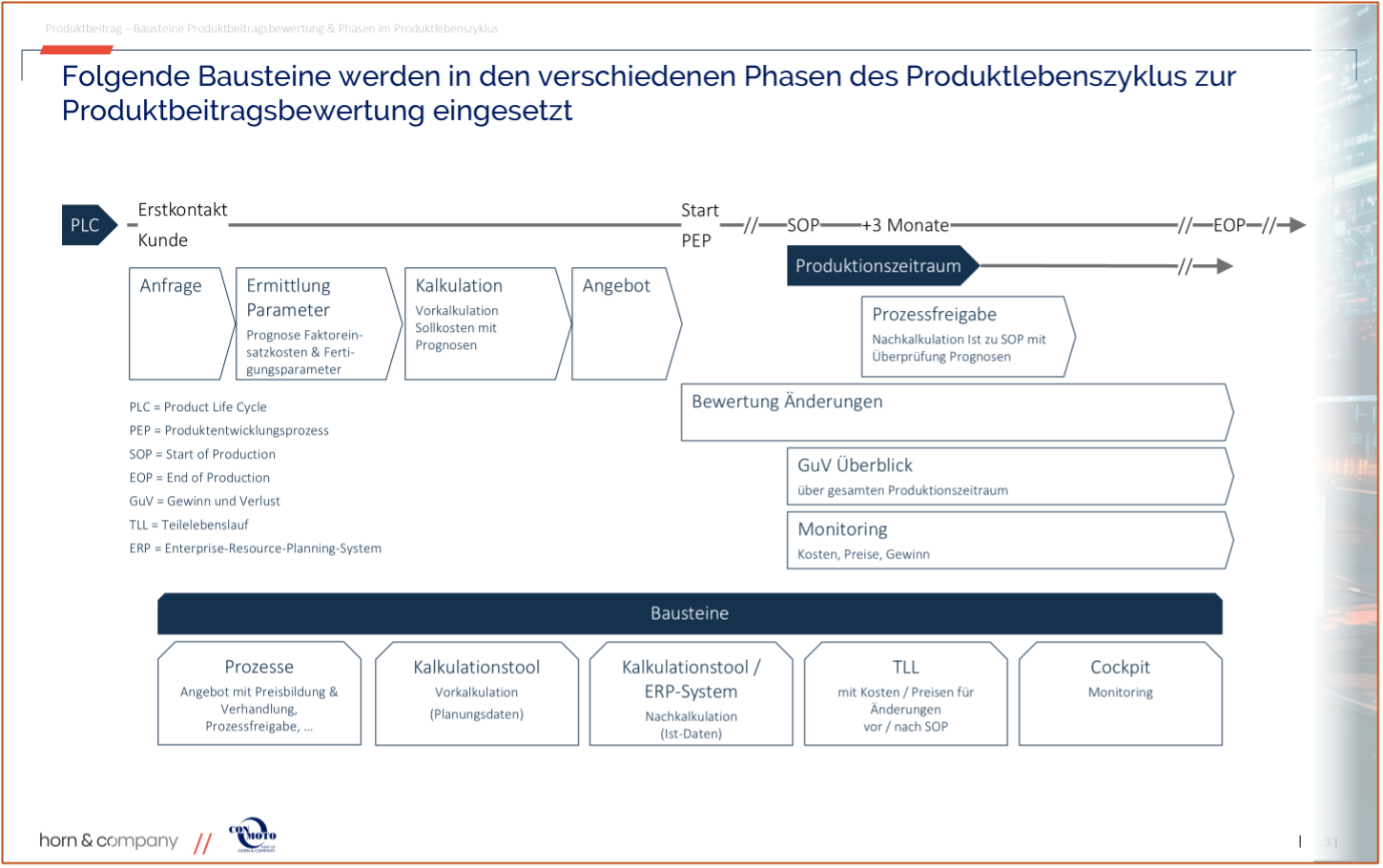
Da sich die Gemeinkosten einem Produkt nicht genau zuordnen lassen, ist es jedoch sehr schwierig, die Kosten und auch den Beitrag pro Produkt zu ermitteln. Eine Kostenträgerrechnung scheint unerreichbar.
Welche Messgrößen sind für die Berechnung notwendig und müssen ermittelt werden? Dazu wird ein Vorgehen vorgeschlagen, den Beitrag pro Produkt näherungsweise gesichert zu ermitteln, falls die Daten einiger Messgrößen fehlen. Dieser modulare Ansatz lässt auch einen späteren schrittweisen Ausbau zu.
Dabei wird der Teil des Produktlebenszyklus (PLC) von der Anfrage bis zur Ersatzteilversorgung aus Sicht des Herstellers betrachtet. Der Artikel befasst sich nicht mit den Kosten über die gesamte Produktnutzungsdauer im Sinne eines Total Cost of Ownership (TCO). Es werden allein die Kosten und Preise der Herstellung betrachtet. Folgekosten nach Produktionsende, die aus der Perspektive des Nutzers bei der Nutzung oder im Gewährleistungsfall entstehen, gehören nicht zum Inhalt des vorgeschlagenen Controllings pro Produkt.
Ansatz Produkt-Monitoring – Cockpit
Der Produktlebenszyklus beginnt mit der Anfrage. Nach einer Machbarkeitsanalyse wird die Entscheidung über die Abgabe eines Angebots gefällt. Dann erfolgt eine Kalkulation für das Angebot. Noch vor Produktionsstart werden bereits Teileänderungen mit weiteren Kalkulationen bewertet. Solche Nachkalkulationen bei Änderungen erfolgen über die gesamte Produktionszeit bis zum Produktionsende inklusive der Ersatzteilbewertung.
Die Auslöser dafür sind zum einen technische Änderungen (z. B. Produktkonstruktion,
-anforderungen oder Materialwechsel), zum anderen Änderungen in den ökonomischen Randbedingungen (z. B. angefragtes Volumen durch fortwährende Korrektur der vorab prognostizierten Stückzahlen, Faktoreinsatzkosten der Einkaufsmaterialien und Medien wie Energie). Alle diese technischen und ökonomischen Änderungen gilt es, in den Kosten und der Preisgestaltung zu berücksichtigen.
Die zu den Änderungen gehörenden einzelnen Kalkulationen ergeben jeweils eine statische Betrachtung zu einem bestimmten Zeitpunkt. Aus diesen Einzelkalkulationen lässt sich eine dynamische Gesamtbetrachtung als Monitoring über den gesamten Produktionszeitraum mit allen geforderten Preisabsenkungen und notwendigen Preissteigerungen aufbauen. Die Vollständigkeit der Bewertung aller Änderungen ist wichtig für den Aufbau des Monitorings.
Diese dynamische Gesamtbetrachtung (Monitoring) lässt sich in einem Cockpit darstellen und reflektiert den Gewinn- und Verlust (GuV)-Beitrag eines Produkts (Produktprofit) zum Betriebserfolg ganzheitlich über den gesamten Produktionszeitraum.
Das Cockpit stellt die Profitabilität des jeweiligen Produkts zum jeweils aktuellen Zeitpunkt dar. Zu diesem Zweck werden bereits in der Vergangenheit liegende Zeiträume mit Istwerten kalkuliert, während für zukünftige Zeiträume Planwerte für die Kalkulation prognostiziert werden. Diese Kalkulationen werden in einem Cockpit zusammengeführt, welches die Profitabilität übersichtlich darstellt und als Basis für Unternehmensentscheidungen des Managements dient. Das Cockpit ermöglicht es auch andere Deckungsbeitragsstufen aufzuzeigen.
Operative Umsetzung
Ein solches Cockpit beinhaltet drei Rubriken:
- Preisentwicklung
- Kostenentwicklung
- Gewinnentwicklung
und zwei Hauptachsen:
- Zeitlicher Verlauf in Jahresscheiben sowie Gesamtdarstellung
- Fortführung der Änderungen gem. Teilelebenslauf (TLL)
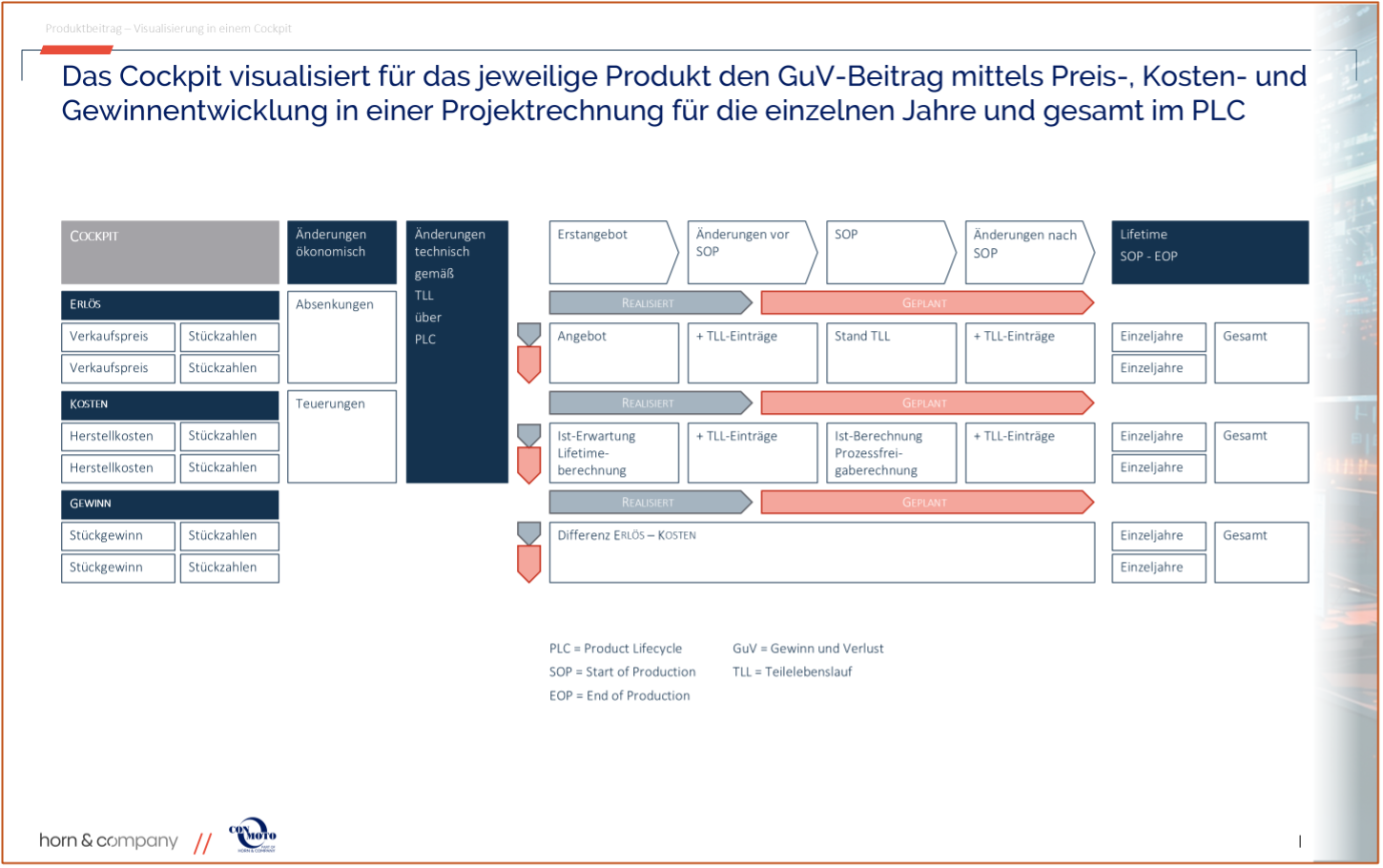
Auf der Kostenseite hält das Cockpit die Kostenentwicklung der Herstellkosten ausgehend vom ersten Angebot über alle Änderungen des Teilelebenslaufes fest. Über die Jahresscheiben können geplante/ realisierte Kostenentwicklungen (z. B. in Zukunft erwartete Teuerungsraten) in der Planung und im Ist dargestellt werden. Zusammen mit den geplanten/ realisierten Stückzahlen pro Jahr und für den gesamten Produktionszeitraum ergeben sich die geplanten/ realisierten Kosten pro Jahr und für den gesamten Produktionszeitraum.
Auf der Preisseite wird im Cockpit die zugehörige Preisentwicklung (z. B. vom Kunden in der Zukunft geforderte Preisabsenkungen) und die sich ergebenden geplanten/ realisierten Erlöse pro Jahr und für den gesamten Produktionszeitraum auf die gleiche Weise wie auf der Kostenseite dargestellt.
Die Darstellung des Produktprofits ist anschließend mittels Differenzbildung einfach möglich und zeigt die geplanten/ realisierten Gewinne/ Verluste pro Jahr und im gesamten Produktionszeitraum.
Mit einer weiteren Unterteilung der Herstellkosten auf der Kostenseite in die variablen und verschiedenen fixen Kosten lässt sich an dieser Stelle über eine Teilkostenrechnung auch der Beitrag zur Deckung der Fixkosten für verschiedene Deckungsbeitragsstufen aufzeigen.
Über die Achse der Änderungen im Teilelebenslauf ist transparent und nachvollziehbar, welche dieser Änderungen für das Unternehmen positive bzw. negative Effekte hatten bzw. haben werden.
Datenermittlung und Beschaffungswege fehlender Daten
Die für das Cockpit notwendigen Daten lassen sich in zwei Gruppen einteilen: Die Daten der ersten Gruppe lassen sich aus dem Blickwinkel der Planung, die der zweiten aus dem Blickwinkel der Ist-Situation ermitteln.
Für die Kostenermittlung zukünftiger Zeitabschnitte (Planung) werden Prognosen der Faktoreinsatzkosten und Fertigungsparameter für die Daten herangezogen, bei bereits in der Vergangenheit liegenden Zeitabschnitten (Ist-Situation) werden die realisierten Faktoreinsatzkosten und Fertigungsparameter als Daten verwendet.
Auf der Preisseite werden für die Planungsdaten die Preise ausgehend von den Kosten über die Ergänzung mit den Gemeinkosten und der geplanten Gewinnspanne gebildet, für die Ist-Daten wird der bekannte Ist-Preis aus der Verhandlung angesetzt.
Bei der Vorkalkulation (Planung) wird das Verfahren der differenzierten Zuschlagskalkulation und ein damit arbeitendes Kostenkalkulationstool verwendet, bei der Nachkalkulation (Ist-Situation) ist alternativ auch eine entsprechende Funktion eines Enterprise-Resource-Planning-Systems (ERP-System) bei Verfügbarkeit einer Kostenträgerrechnung einsetzbar.
Zur Gestaltung des Cockpits ist eine Ergebnisrechnung über den gesamten Produktionszeitraum mit den Stückzahlen der einzelnen Jahre sowie Teuerungen und Preisnachlässen notwendig. Mit diesem Schritt wird das Gesamtergebnis transparent.
Die Bewertung aller technischen und ökonomischen Änderungen wird in einem Teilelebenslauf (TLL) auf Kosten- und Preisseite getrennt dokumentiert. Dieser ist eine weitere Voraussetzung für den Aufbau eines Cockpits.
Zeitliche Fortschreibung – Versionierung des Cockpits
Im Zeitablauf des Produktionszeitraums wird das Cockpit bei allen Änderungen ständig aktualisiert und dafür werden neue Versionen angelegt. Dazu werden im Cockpit die prognostizierten Planungsdaten Schritt für Schritt mit den realisierten Ist-Daten für die realisierten Zeiträume und Teileänderungen ersetzt. Die Auswirkungen auf das Gesamtergebnis im Produktzeitraum sind so zu jedem Zeitpunkt sichtbar.
Vorteile und Möglichkeiten des permanenten Produkt-Monitorings mit einem Cockpit
Ein Vorteil besteht in der übersichtlichen Darstellung. Die Ergebnisse der verwendeten Plan- und Ist-Daten sind in ihrer Auswirkung für das Produktergebnis an einer Stelle transparent.
Ein weiterer Vorteil besteht in der eindeutigen Dokumentation aller Änderungen und zudem durch die verschiedenen Versionen im zeitlichen Fortschritt, wenn prognostizierte Daten (Planung) durch realisierte Daten (Ist-Situation) ersetzt werden.
Das Cockpit zeigt auf, welche der Annahmen sich bewahrheitet haben und welche Auswirkung diese bei Realisierung erzielt haben.
Über diese Darstellung hat das Management den Produktergebnisbeitrag zum Betriebserfolg jederzeit im Blick und ist in der Lage, Korrekturen einzuleiten.
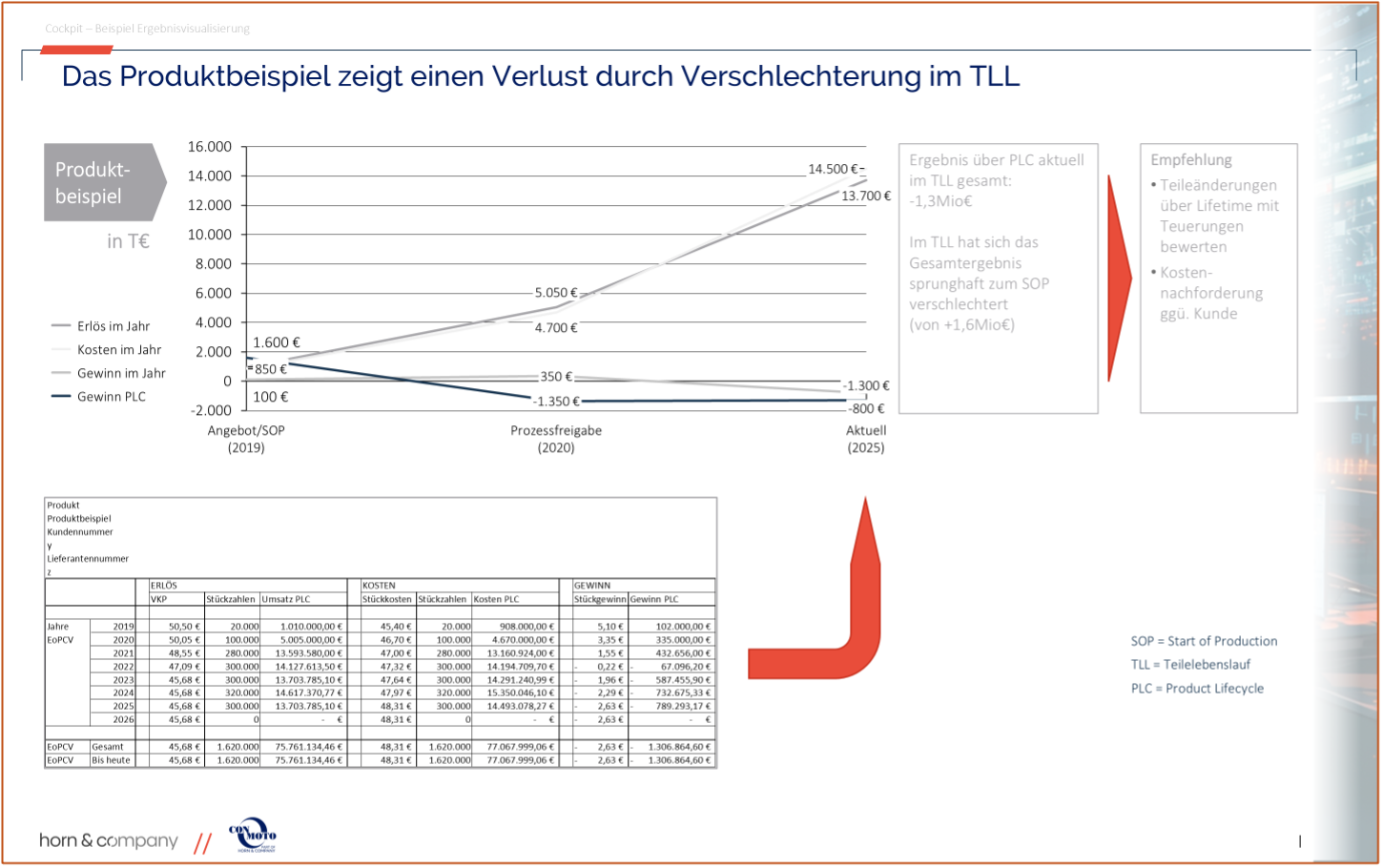
Weiterhin bietet das Cockpit die Möglichkeit der Simulation potenzieller Anpassungen oder notwendiger Maßnahmen.
Anpassungen können aus Teuerungen der Einsatzfaktorkosten oder Preisabsenkungen durch den Kunden bestehen. Notwendige Maßnahmen können sich aus geänderten Betriebsumständen (z. B. geänderter Fertigungsablauf oder -verfahren) ergeben.
Das Management kann die Auswirkungen der Anpassungen oder Maßnahmen überprüfen und ist in der Lage, Entscheidungen zu treffen.
Das Cockpit zeigt auch, ab welchen Parametern das geplante Gewinnziel in Gefahr gerät oder der Deckungsbeitrag unter eine kritische Schwelle fällt.
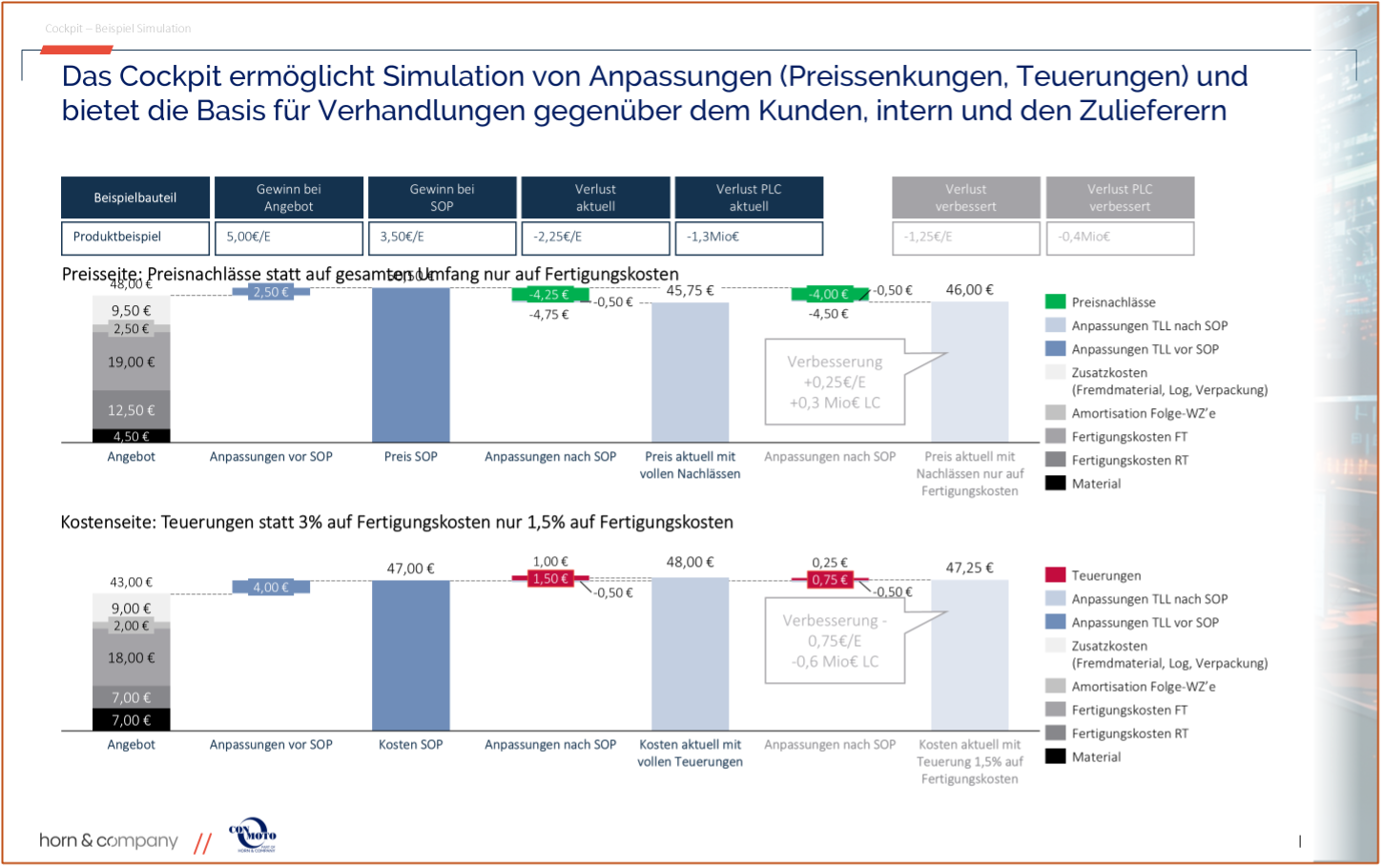
Einsatz Differenzierte Zuschlagskalkulation beim Produkt-Monitoring
Die Vorteile eines Einsatzes der differenzierten Zuschlagskalkulation für das Produkt-Monitoring liegen in
- einer größeren Systemunabhängigkeit
vor allem vom Vorhandensein eines ERP-Systems bzw. von der Datenqualität in einem ERP-System für die Ermittlung der realisierten Daten (Ist-Situation) - der Adaptierbarkeit
z. B. neue, bisher von der Firma nicht angebotene Produkte mit neuen, nicht vorhandenen Fertigungsabläufen zu kalkulieren (Planung) - der Gestaltungsfreiheit
wie tiefgehend Kosten als Einzelkosten ermittelt und dem Produkt zugewiesen werden
Diese Kalkulationsmethode lässt sich sowohl für die prognostizierten Werte (Planung) als auch die realisierten Werte (Ist-Situation) anwenden. Zudem verlangt sie bei der Anwendung keine vollständige Betrachtung des gesamten Unternehmens bzw. des Produktspektrums.
Zudem können anstatt nicht vorhandener Ist-Daten bis zu deren Vorliegen weiter einfach Planungsdaten bzw. logische Ableitungen davon verwendet werden. Bei den automatisierten Abläufen einer Kalkulation mit einem ERP-System ist dies nicht oder nur aufwändig möglich.
Fazit Produkt-Monitoring
Der Ansatz ermöglicht Unternehmen, ein produktergebnisbezogenes Monitoring modular und mit einer hohen Systemunabhängigkeit aufzubauen. Dabei können vorhandene Elemente der Planungskalkulation und des Ergebniscontrollings verwendet und fehlende ergänzt werden.
Mit Hilfe des sich ergebenden Cockpits kann zu jeder Zeit der Gewinn- und Verlustbeitrag (Profitabilität) eines Produkts über den gesamten Produktionszeitraum prognostiziert und visualisiert werden.
Welchen Mehrwert hat ein solches Produkt-Monitoring?
- Überblick Produktprofitabilität über gesamten Produktionszeitraum
- Übersichtliche Darstellung (Gesamtüberblick im Cockpit)
- Guidance durch systematischen Aufbau (Vollständigkeit & Fehlervermeidung)
- Modularer Aufbau (Verwendung bestehender Bausteine mit Ergänzung fehlender)
- Flexibilität in Datenermittlung und -verarbeitung
- Simulationsmöglichkeiten von Änderungen
Durch diesen Ansatz kann vermieden werden, dass aus rein statischen Betrachtungen nicht korrekte Gewinn- und Verlustbeiträge für einzelne Produkte ausgewiesen werden und anschließend nicht zum gesamtheitlich ermittelten Betriebsergebnis passen.
Ebenfalls ermöglicht der Ansatz als Entscheidungsbasis eine Steuerung auf der Produktebene, von operativen Korrekturmaßnahmen bis hin zur strategischen Planung beim Produktportfolio des Unternehmens.